ADDIT BV
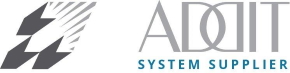
Archimedesweg 2
5928 PP Venlo
Industrienummer 4145
Tel. (077) 3203400
Fax (077) 3874535
E-mail: info@addit.nl
Website: www.addit.nl
Addit: Parallel engineering en slimme IT-systemen verkorten time-to-market
High Mix, Low Volume en High Complexity, dat zijn de drie productiekenmerken waar alles om draait bij plaatverwerkingsbedrijf Addit in Venlo. Het bedrijf fabriceert hoogwaardig precisie plaatwerk en ontwikkelt (assemblage)concepten voor samengestelde modules, apparaten en machines. Met de modernste technologieën bedient Addit klanten in 16 verschillende Europese landen, verdeeld over 12 uiteenlopende sectoren. De afgelopen jaren is fors geïnvesteerd in een nieuwe IT-infrastructuur, zodat alle medewerkers, van de ontwerptafel tot de werkvloer, altijd en overal inzicht hebben in de meest actuele productinformatie.
Addit heeft 2 vestigingen: in Venlo werken 55 mensen, in het Poolse W?grów maar liefst 800. In Nederland ligt de focus op innovatie en nieuwe markten en gaat het vooral om producten die nog aan het begin van hun lifecycle zitten. In Polen richt men zich meer op de seriematige productie van al langer bestaande producten. Maar seriematig betekent in de wereld van Addit niet dat er duizenden dezelfde standaardproducten van de band rollen. “Wij produceren uitsluitend in lage volumes”, legt directeur Peter Kerstjens uit. “Wij hebben de meest moderne plaatverwerkende technologie in huis om zo efficiënt mogelijk en in zo kort mogelijke tijd heel veel verschillende (high mix), ingewikkelde (high complexity) producten te produceren in kleine aantallen (low volume). Het meest ideale binnen het lean manufacturing is de one piece flow: één product maken en leveren precies op het moment dat de klant het nodig heeft. Dat kan natuurlijk niet altijd, maar dat ideaalbeeld benaderen wij een heel eind.”
Berg aan technologie in één product
Als voorbeeld van een high complexity product noemt Kerstjens een machine die zij hebben ontwikkeld en gemaakt voor een productielijn van brillenglazen, die 24/7 duizenden brillenglazen per uur produceert. “Onze machine staat aan het einde van de productielijn en moet de geslepen en gepolijste brillenglazen los trillen van een kunststof houder d.m.v. een 150 bar pulserende waterstraal. De linker en rechter brillenglazen komen terecht in verschillende bakjes en worden door een robot verpakt. De houders worden hergebruikt. In deze machine zit zoveel technologie verwerkt: optica, software, elektronica, pneumatiek, waterhuishouding... noem ze allemaal maar op. In totaal zijn er zo’n 4.000 verschillende onderdelen in verwerkt.” Addit produceert 15 tot 20 van deze machines per jaar in de fabriek in Venlo.
Parallel engineering in walhalla van hightech kennis
De brillenmachine werd onder hoge tijdsdruk in slechts 6 maanden ontwikkeld, maar de meeste ontwikkeltrajecten duren langer. “Wij doen er alles aan de ‘time-to-market’ van een product zo kort mogelijk te houden”, vertelt Kerstjens. “We hebben het grote voordeel dat heel veel leveranciers en ontwikkelaars van componenten die wij nodig hebben, hier in deze hightech regio van Zuidoost Nederland zitten. In de driehoek Leuven-Eindhoven-Aken is een ongelooflijke hoeveelheid kennis aanwezig op allerlei gebieden. Door dat open en toegankelijke ecosysteem kunnen wij met onze partners parallel engineeren. Dus naast elkaar werken we gelijktijdig ieder aan een deelmodule van het product. Internationaal gezien is dat echt de grote toegevoegde waarde van de Nederlandse maakindustrie. Ja, als het moet, dan kunnen we verrekte snel zijn!” voegt hij er trots aan toe.
Hoge eisen aan toeleveranciers
De ruim 300 klanten waar Addit voor werkt zijn allemaal OEM (Original Equipment Manufacturers). Peter Kerstjens ziet dat deze bedrijven zich in het afgelopen decennium steeds meer gingen richten op hun core business: R&D en Sales&Marketing. “Voor een OEM is het onmogelijk om alle technologieën en ontwikkelingen zelf te volgen, dat gaat in deze tijd razendsnel. Dus zoeken zij goede partners, zoals Addit dat is voor het plaatwerk. Dat betekent dat er van de toeleveranciers veel meer gevraagd wordt dan 20 jaar geleden. We worden nu veel eerder betrokken in het ontwikkelproces en kunnen vanaf het begin onze kennis en kunde inbrengen. Dat is een heel goede zaak, die ook bijdraagt aan een fijne relatieopbouw met de klant.”
Goede IT tools onontbeerlijk
Om al deze complexe zaken voor veel verschillende klanten in de diverse life cycle stadia in veel verschillende segmenten goed te managen, heb je een goede IT infrastructuur nodig. Met moderne tools, die je mensen in staat stellen te voldoen aan de toenemende druk om steeds sneller te leveren en steeds sneller informatie uit te wisselen.
Alle kennis direct toegankelijk voor iedereen
Addit investeerde in de afgelopen 3 jaar fors in zulke nieuwe IT tools. Na een gedegen onderzoek kochten ze het software pakket ProFile van PML Expert. Dit is een PDM (product data management) systeem waarin alle technische informatie per klant en per product compact en helder is opgeslagen. Het duurde 2 jaar voordat alle technische informatie van alle producten was ingevoerd en de medewerkers intensief getraind waren in het gebruik. Alle wijzigingen die worden gemaakt worden direct gedocumenteerd. Van alle projecten is er te allen tijde up to date transparante informatie beschikbaar. Of zoals Peter Kerstjens het verwoordt: “Voorheen zat de kennis over een project voor een deel in tientallen ordners van een engineer en voor een deel in zijn hoofd. Nu zit alle kennis in het systeem en is voor alle betrokkenen direct toegankelijk.”
Altijd de meest recente productinfo
In een tweede fase werd ook een nieuw ERP systeem geïmplementeerd. Addit koos voor Ridder IQ, omdat dit goed aansluit op het ProFile software pakket. “Het was voor ons heel belangrijk dat wij alle technische data uit PDM geautomatiseerd kunnen transformeren naar het ERP systeem”, vertelt Kerstjens. “Daarnaast hebben we ook geïnvesteerd in een apart shopfloor systeem. Hiermee kunnen we alle productinfo gedigitaliseerd aanbieden aan onze medewerkers op de productievloer. Soms gaat dat via pc’s die aan machines vastzitten, maar we hebben ook 24 mobiele werkstations die overal in de fabriek kunnen worden neergezet. Op deze wijze beschikken onze medewerkers altijd over de meest recente technische documentatie. Ze kunnen gemakkelijk data terugvinden, instructies ophalen, video’s terugkijken of communiceren met engineers om verbeteringen door te geven. Ordermappen met allerlei tekeningen of dikke documenten met assemblage instructies: het behoort gelukkig allemaal tot het verleden.”
Nu de kinderziektes eruit zijn gaat Addit in 2020 volgende stappen nemen om de IT systemen verder te optimaliseren. “Nu gaan we de echte winst pakken”, verzekert Kerstjens. “Eerst hebben we onze medewerkers aangehaakt, dit jaar gaan we de toeleveranciers aan onze digitale processen koppelen. Je ziet vaak dat bedrijven na een implementatie maar zo’n 30% van de potentie van het systeem benutten. Dat gaat bij ons echt niet gebeuren!”
Auteur: Dianne Huijskens